
Thermal study: reactor materials will be printed on a 3D printer
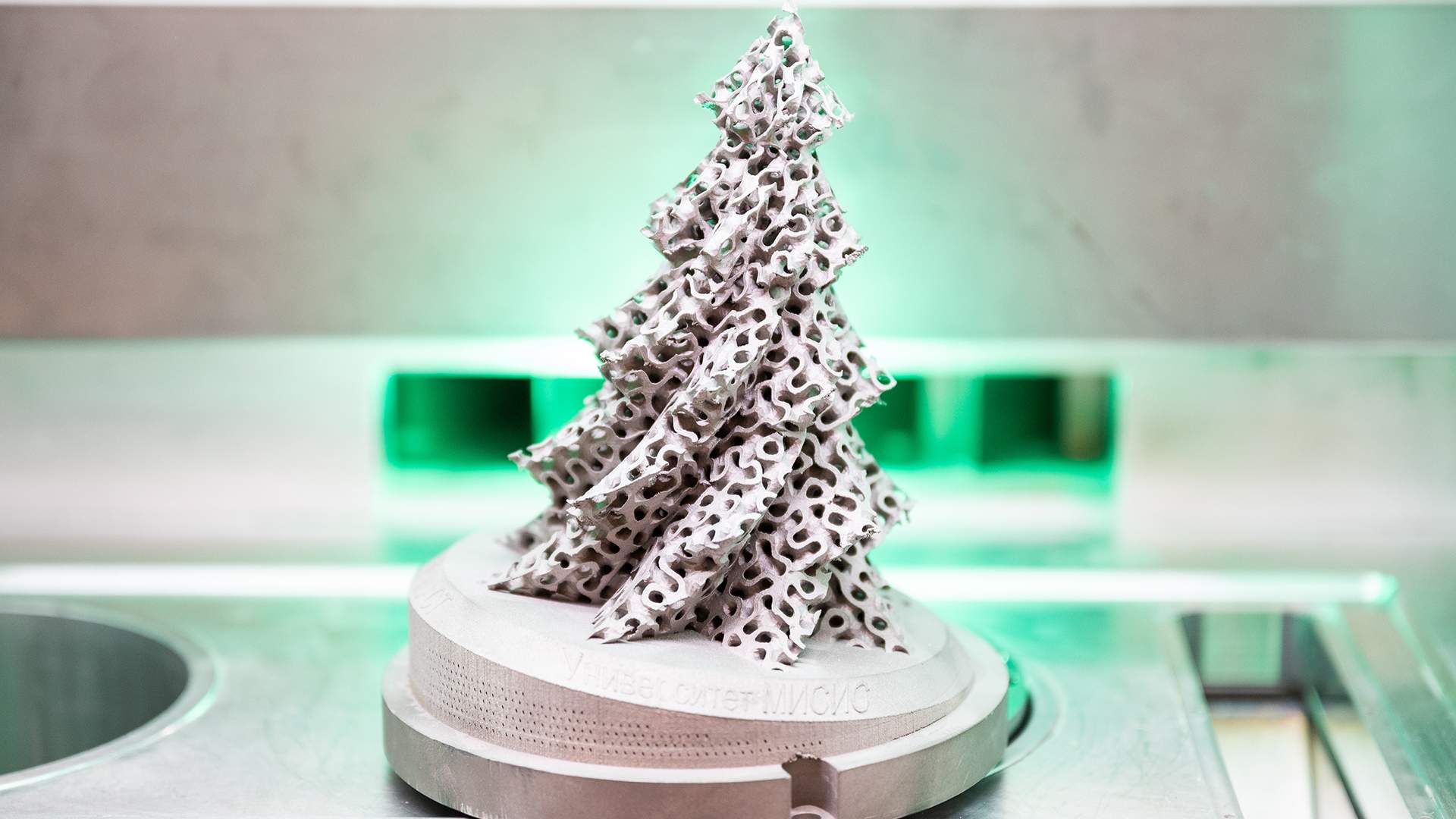
Russian scientists have developed a new technology for the production of materials to create elements of fusion reactors. We are talking about components facing the plasma in power plants. They are exposed to a powerful impact, so they must have very high characteristics. With the help of 3D printing, experts have obtained a composite of copper and tungsten, which combined the advantages of both metals. According to experts, the search for suitable materials is one of the most pressing issues in the development of fusion plants, and their solution brings the era of thermonuclear energy closer.
Material for interaction with plasma
Specialists of NITU MISIS together with colleagues from NIIEFA JSC have proposed a new method of production of materials for plasma-facing components in fusion reactors. These parts are subjected to heavy loads, such as high temperature and exposure to hydrogen isotopes, so their properties are subject to special requirements. Hybrid technology, which combines additive manufacturing (3D printing) with classical approaches, produces a bimetallic composite of tungsten and copper with improved characteristics. It significantly exceeds the capabilities of analogs used today.
- Research and development of new methods for manufacturing tungsten parts is of high practical importance. Selective laser melting technology (3D metal printing - Izvestia) is one of the most popular and used methods of additive manufacturing of metal products due to the possibility of synthesizing complex-shaped parts with high resolution. Production of tungsten products using this method is a difficult task due to high melting temperature, formation of non-melting defects, microcracks and overheating of various units in the installations, - noted Stanislav Chernyshikhin, Head of the Laboratory "Catalysis and Hydrocarbon Processing" at MISIS University.
A thermonuclear reactor is a facility in which energy is produced by self-sustained controlled thermonuclear fusion. It allows generating much more energy than the nuclear fission reaction, which is used in modern nuclear power.
So far, only research reactors of this type exist. However, work on creating the first copy for practical use is being carried out all over the world. The most famous international project in this field is ITER (International Thermonuclear Experimental Reactor). Its construction began in 2010, and it should be completed in 2035. A modernized T-15MD fusion reactor for research purposes is operating at the Kurchatov Institute. The creation of new materials for such facilities brings the era of thermonuclear energy closer.
Tungsten is considered one of the main materials for plasma-facing components due to its high melting point and other important characteristics. However, it is difficult to machine due to its high hardness and brittleness. To fabricate a tungsten component, classical powder metallurgy methods are usually used, but they do not allow the creation of complex-profile products. Therefore, the traditional design of these elements is a simple multilayer construction. Additive manufacturing makes it possible to synthesize a product layer by layer, including those with a given porous structure, MISIS said. The properties of such components can be adapted for a specific task by changing their geometric structure, the specialists explained.
The team of NITU MISIS managed to obtain the relative density of solid samples in 96.7% with the help of laser synthesis . First, tungsten porous structures were fabricated by selective laser melting to create the composite. Then copper was added to the matrices at temperatures up to 1350°C. By studying the wetting and kinetics of copper impregnation of the tungsten matrices, the scientists established the optimal conditions for this operation.
When the application of fusion begins
It is known that pure tungsten is a brittle metal. With minor deformations in the material, cracks appear. However, mechanical tests showed that the resulting composite was much more ductile - no fracture was observed at a deformation of 35%. This is very important in the production of plasma-facing components.
-In the future, we plan to move to the production of mock-ups of plasma-facing components and heat-loaded cyclic tests. The tests will simulate impacts close to real operating conditions in fusion plants," said Stanislav Chernyshikhin.
The choice of cladding material is one of the most acute issues in the development of fusion plants. It must be able to withstand huge flows of heat and particles, and neutron damage is added under reactor conditions, Yuri Gasparyan, acting head of the Department of Plasma Physics at MEPhI, explained to Izvestia.
- Plasma-facing elements are usually made of several materials, which adds to the problem of their reliable connection. The new development by MISIS and NIIEFA using additive technologies makes it possible to create a composite material of tungsten and copper and makes it possible to achieve the advantages of each of the materials and organize a special internal structure, " he said.
In the future there is still a lot of work to be done to optimize the technology to reduce the porosity of the material and to study the functional properties of the material under thermal and plasma exposure. After that it will be possible to speak more accurately about the prospects of this solution, the scientist added.
According to Alexei Belogoriev, Head of the Expert Analytical Department for Fuel and Energy Complex of the Institute of Energy Strategy, the development of solutions for fusion reactors is necessary, but their practical application is possible only on the horizon of several decades.
- All leading countries aiming at space exploration are engaged in the development of fusion reactors, as this type of energy is well suited for space flights. And if Russia wants to remain a leader in this field, it is necessary to develop the technology. For civilian energy, it is necessary for fusion to be economically profitable. None of the experts take it into account in forecasts until 2050, because the uncertainty associated with this approach is still very high," he said.
In any case, it is a very important source of low-carbon energy because it is much more efficient than renewables and nuclear power. Therefore, research needs to continue, but for now it is at a fundamental stage, the specialist emphasized.
Переведено сервисом «Яндекс Переводчик»