- Статьи
- Science and technology
- Union of Composites: tests of mini-samples of materials will accelerate the creation of aircraft

Union of Composites: tests of mini-samples of materials will accelerate the creation of aircraft
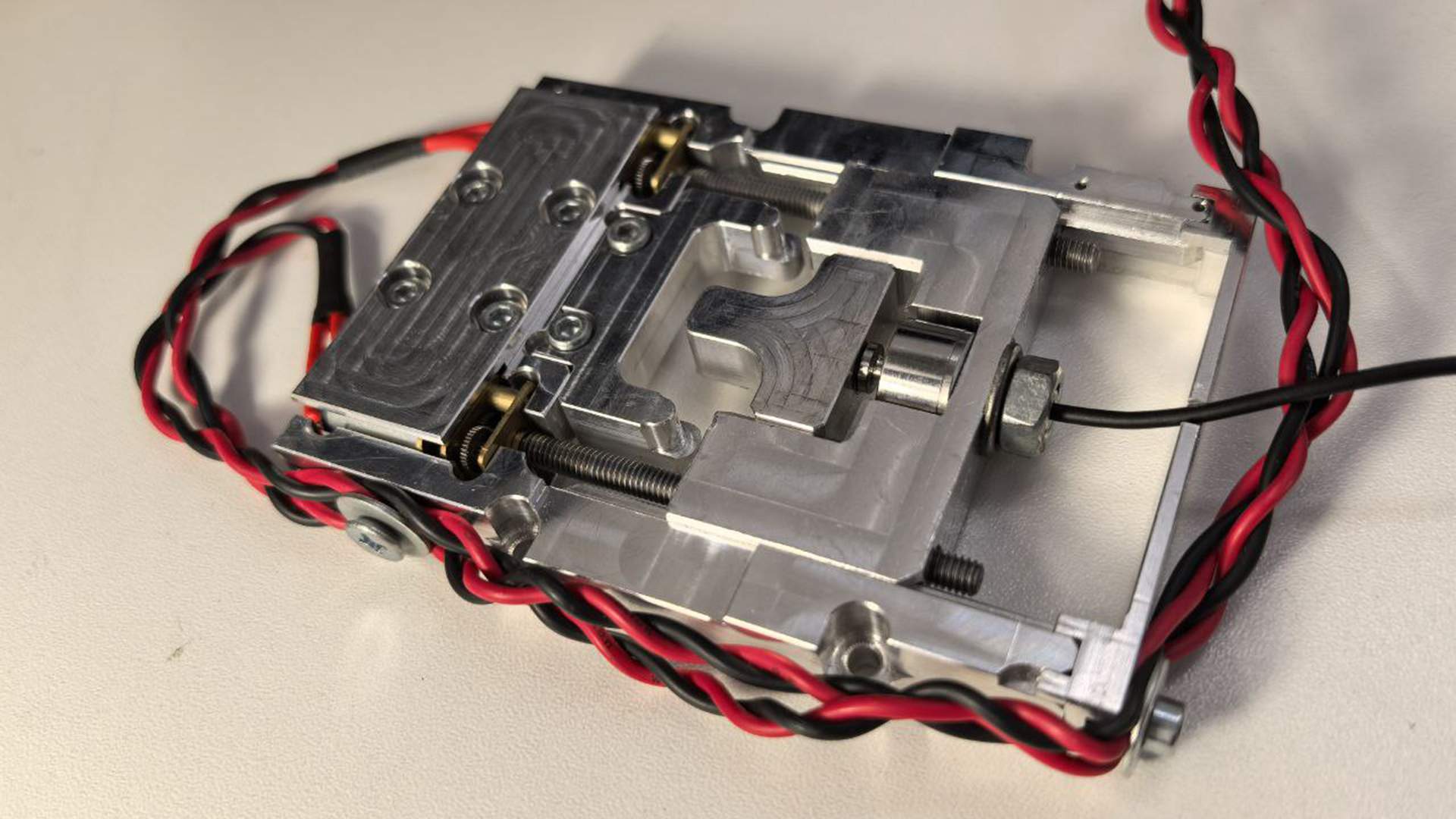
Russian scientists have proposed a new technology for testing aviation and aerospace composite materials. It includes conducting tests on miniature samples in combination with computational modeling. The technology will help to increase the number of tests and reduce their cost. This will make it possible to accelerate the development of new aircraft and spacecraft, experts say.
What is the difference between composites and metal alloys?
Scientists from the Skolkovo Institute of Science and Technology, the Moscow Aviation Institute and the National Research University of Technology MISIS have developed an innovative technique for testing the strength of polymer composites reinforced with carbon fiber. Such materials are widely used in the modern aviation and aerospace industries. The new method involves conducting research on a volume of about 1 cm3 of material.
As the developers explained, polymer composites are strong enough and resistant to deformation, which reduces the weight of structures made from them (for example, compared with aluminum alloys). However, a number of problems limit the use of these materials. In particular, their destruction processes are much more complicated than in metal alloys, which are traditional for aviation and astronautics. This requires a revision of computational and experimental approaches.
— For example, for metals, it is enough to know their chemical composition and the history of thermomechanical processing in order to predict the basic mechanical characteristics of the samples and the behavior of the material in the finished product. This will not work with composites: their properties at the level of the sample and the finished product may differ significantly. To ensure the stability of the properties of carbon composites, it was proposed to start studying them at the micro level, and then transfer these data to larger objects using computer modeling and rational experiment. This will avoid the need to produce huge samples each time and load them to destruction in order to understand how the material works," Alexey Salimon, one of the developers, deputy head of the NUST MISIS Accelerated Particle Laboratory, told Izvestia.
How research is conducted on mini-samples of material
He explained that a special laboratory testing facility has been developed to implement the technology. It can be placed, for example, inside a scanning electron microscope. The device is a special frame on which various parts are fixed: a force sensor, micro motors and drives. They are controlled remotely through a special port in the vacuum chamber of the scanning electron microscope.
During the tests, the scientist said, miniature samples are fixed to the frame in grips and deformed in a controlled manner. The maximum force with which it is possible to affect the material is about 50 kilograms of force (the weight of a kilogram at standard gravity). The device allows for bending, stretching and compression tests.
— Materials produced by an additive method, such as composites, have strong anisotropy of properties (uneven physical properties of the body inside it). Traditionally, tests are carried out on large samples, which requires significant material consumption and complex experimental facilities. We have shown that these data correspond to those that can be obtained from miniature samples. Moreover, the latter are easier and cheaper to manufacture, and if you have a large number of them, you can conduct many tests and collect a large statistically significant amount of data," explained Evgeny Statnik, a researcher at the Skoltech System Design Center.
At the next stage, he specified, the data obtained will be used for computational and experimental correlation, that is, confirmation of mathematical models. This combination of experimental and computational data makes it possible to minimize errors and gain a more complete understanding of the properties of the material.
At the same time, the researcher noted, the researchers record all the changes that occur in the material using digital cameras. At each loading step, an exceptionally high-resolution image is obtained.
As the developer and designer explained, this allows real-time observation of deformations and structural disturbances of polymer composites at the level of individual fibers and the epoxy matrix. It is worth noting that the size of one carbon fiber is about 5-7 microns, and the epoxy layer between them is also units of microns.
— The sources of damage and vulnerability of the material lie precisely in its microstructure and small-scale deformations. We have applied our own algorithms to analyze digital video data, which allow us to see the nuances of strain concentration based on the detailed images obtained in the microscope and determine the types of defects that caused the deterioration of the properties of the sample under study," explained Professor Alexander Korsunsky, head of the Laboratory of Hierarchically Structured Materials at Skoltech.
Ultimately, he stressed, these data help to accurately locate and predict the origin and development of damage. This makes it possible to reliably calculate the strength of the material in order to achieve its required characteristics even at the development stage. And this, in turn, will accelerate the development of new aircraft and spacecraft.
Study of microprocesses in the material
— The properties of epoxy matrix polymers reinforced with carbon fiber depend on many factors. For example, it depends on the direction of the reinforcing fibers, their combination with the binder, and so on. Therefore, the safe use of composites in aviation and aerospace materials science requires comprehensive study and repeated testing," said Evgeny Kurkin, Senior Researcher at the Department of Aircraft Design and Engineering at Samara National Research University named after Academician S.P. Korolev.
According to him, reducing the size of the samples will increase the number of experiments and increase statistics. As a result, engineers will be able to draw more accurate conclusions at a lower cost. Similar studies are being conducted in other research institutions, including Samara University.
— The development is necessary to analyze the micro-processes that occur in composite materials under load. Such data is very valuable, as knowledge of the mechanism of the process makes it possible to control it," commented Evgeny Alexandrov, Director of the NTI Center for Digital Materials Science: New Materials and Substances at Bauman Moscow State Technical University.
For example, he said, it is possible to determine the balance between surface wettability, adhesion (adhesion of surfaces of dissimilar solid and/or liquid bodies) at the interface between the filler and the matrix, and the roughness necessary to prevent the fiber from slipping out of the matrix under load.
There are computer systems for modeling such processes, but there has always been a big question about how much the model matches the real object. The proposed methodology makes it possible to combine these data, the expert concluded.
— The main advantage of composite materials in aviation and space is their high specific strength, which saves the weight of an aircraft or spacecraft. It is also possible to profitably use local anisotropy (internal unevenness). For example, we can arrange the reinforcement so that the maximum strength of the structure is demonstrated precisely in the direction of applying the main load," said Artur Gareev, Deputy Director for Science and Innovation at NIIgrafit JSC.
However, he noted that the use of very small samples may conflict with the very structure of the material. For example, there will be a loss of contact between the reinforcement threads and the binder, which will prevent the strength of the composite material from being fully realized.
According to the expert, a complete set of equipment will have to be created separately for the scale model, which will also require additional costs. In general, in simple loadings, where such a technique can be used with a sufficient degree of confidence, there is actually no need to verify calculations on large-scale samples. A well-conducted calculation for such cases will coincide very closely with the result of the actual load, he added.
Переведено сервисом «Яндекс Переводчик»